The spark-ignition 4-cycle engine burns a mixture of AIR and FUEL. The
air is controlled by the driver's operation of the throttle. The fuel is
mixed with the incoming air by the carburetor. The Ratio of AIR to FUEL is
the AIR/FUEL Ratio (A/F). This is a ratio by WEIGHT; if 12 pounds of Air
are combined with 1 pound of Fuel the A/F is 12:1, or more commonly, A/F =
12.
Despite the enormous variety in engine designs, virtually all
(spark-ignition 4-Cycle) engines have very similar A/F Ratio requirements.
For fully warmed-up engines, the range of A/F is:
A/F RATIO
|
CHARACTERISTICS
|
5 to 1
|
RICH BURN LIMIT: Combustion is weak/erratic.
|
6-9 to 1
|
EXTREMELY RICH: Black smoke and low power.
|
10-11 to 1
|
VERY RICH: Some supercharged engines run in this range at
full power as a means of controlling detonation.
|
12-13 to 1
|
RICH: Best power A/F: Un-supercharged
WOT.
|
14-15 to 1
|
CHEMICALLY IDEAL: At 14.6 the A/F is at the theoretical
ideal ratio with no excess fuel or oxygen after combustion. Good
A/F for part throttle cruise and light to moderate acceleration.
|
16-17 to 1
|
LEAN: Best economy A/F ratio. Borderline for part
throttle drivability (worse than borderline if EGR is used).
|
18-19 to 1
|
VERY LEAN: Usual lean limit
(Driveability).
|
20-25 to 1
|
LEAN BURN LIMIT: Varies with engine and system.
|
Even though engines will run anywhere between 5 and 25 A/F, the usual
target values for an un-supercharged engine are a fairly narrow range
(Figure 1). A/F is about 12.5 for the WOT and 14.0-15.5 at part-throttle
cruise. An intermediate value of about 13.5-14.0 is usually used for
mid-range power (non-WOT acceleration).
The Edelbrock carburetor has three (3) basic systems that meter
fuel to the engine: The Idle System, Primary Main System, and
Secondary Main System. By understanding the operation of each you will
be better prepared to calibrate your carburetor.
Idle System: The Idle System delivers 100% of the idle fuel. It
also meters fuel at off-idle throttle positions; a large percentage at
just off of idle decreasing to a minor influence as the throttle is
opened wider. The idle setting is critical both to a smooth idle at
proper rpm and to a smooth transition to part-throttle operation.
Fuel is drawn through the Idle System (Figure 2) by the intake
manifold vacuum that is communicated at the Idle Screw Port (8) and
Transfer Slot (7). Fuel in the bowl passes through the Primary Main
Jet and Metering Rod Restriction (1) and into the Primary Well (2).
The fuel for the Idle System is drawn through the restriction at the
end of the Idle Jet (3) - a brass tube - and flows up the tube to the
location of the 1st Idle Air Bleed (4) - a brass restrictor - where
air is mixed with the liquid fuel. The emulsified air and fuel is then
drawn through the Idle Channel Restrictor (5) - a drilled passage that
serves to increase the velocity of the air and fuel to promote better
mixing. As the emulsified fuel is discharged from the Idle Channel
Restrictor, additional air is added at the 2nd Idle Air Bleed (6) - a
drilled hole - and the highly aerated mixture then moves through the
passages in the main-body to the location of the Transfer Slot (7) and
Idle Screw Port (8). The Transfer Slot (7) is a large air bleed when
the throttle is closed, but as the throttle is opened the slot is
exposed to manifold vacuum and becomes a discharge port for Idle
System fuel. The Idle Screw Port is a variable discharge restriction
that is adjusted by the engine tuner to achieve the desired A/F Ratio
at engine idle.
Primary Main System
The Primary Main system delivers an
increasing percentage of the fuel as throttle position increases
(phasing over the Idle System) and varies fuel delivery in response to
air flow and manifold vacuum.
Fuel is drawn through the Main System (Figure 3) by the
pressure-drop that occurs when the incoming air flow must increase in
velocity in order to pass the reduced throat areas at the Main Venturi
(1) and the Boost Venturi (2). This pressure-drop (or suction) is
communicated to the system by the Nozzle (3)-a brass tube that opens
into the inside of the Booster Venturi (2).
The fuel must pass through the restriction at the Main Jet (4) and
Metering Rod (5). The Rod extends through the Jet, reducing the amount
of area available for fuel flow. If the diameter of the Rod is large,
then fuel flow through the Jet is more restricted than if the Rod were
small.
After the Rod and Jet, the fuel enters the Primary Well and is
drawn up the inside of the Primary Well Tube (6). Sometimes this tube
is called an Emulsion Tube. Here, the fuel is mixed with air that
enters the inside of the Tube through a series of small holes. The air
is supplied by the Main Well Bleed (7) at the top of the Main Well.
The air/fuel mixture exits from the top of the Main Well into a
passage that leads it to discharge into the Booster Venturi (2) at the
Nozzle (3).
The fuel flow rate in the Main System is proportional to the air
flow rate; as air flow increases - from either an increase in throttle
opening or an increase in engine speed at the same throttle opening -
the fuel flow also increases by nearly the same degree.
At higher engine loads, such as in a heavy part-throttle
acceleration, there is a need for a richer mixture. This enrichment is provided by the Metering Rod and
Step-Up Function (Figure 4). A vacuum passage (8) communicates the
manifold vacuum to the underside of the Step-Up Piston (9). This
vacuum tries to hold the Piston in the bottom of its bore by working
against the force of the Step-Up Spring (10).
When the manifold vacuum is high, indicating a low load such as
idle, cruise, or light acceleration, it is able to overcome the force of the Step-Up
Spring and hold the Step-Up Piston at the bottom of its bore, which
also positions the Metering Rod at the bottom of its travel. At this
point, the Rod has a large diameter that creates a high restriction
through the Jet and the fairly lean A/F Ratio that is desirable for
low load/low power operation. This portion of the Metering Rod is
referred to as the "Lean Step" of the Rod.
When the manifold vacuum is low, indicating a high load such as a
heavy part-throttle (or WOT) acceleration, the Step-Up Spring is able
to force the Piston to the top of its bore and position the Metering
Rod at the top of its travel. This action is called "Power Mode
Staging". The portion of the rod now located in the jet has a
smaller diameter, thus the restriction through the Jet is reduced and
a rich A/F Ratio is provided for high load/high power operating
conditions. This is the "Rich Step" of the Rod.
Secondary Main System
The Secondary Main System (Figure 5)
delivers fuel only when the secondary throttle blades and air valve
are open. It ensures that fuel delivery varies with air flow.
The Secondary Throttles (1) begin to open when the Primaries are
about 65% open. The Primary and Secondary Throttles arrive at the WOT
stop at the same time.
Air flow through the Secondary side is controlled by Air Valves
(2). These valves are located in the secondary bores above the
throttle blades. They are balanced against a counter weight and open
to admit additional air flow only if there is enough air velocity to
allow the proper operation of the Secondary Metering Systems.
The principles of operation for the Secondary Main System are the
same as those that govern the operation of the Primary Main System;
the pressure drop (suction) arises from the increase in the airs
velocity as it passes through the Venturi sections. The pressure drop
(suction) at the Secondary Booster Venturi (3) is communicated into
the system by the Secondary Nozzle (4).
Fuel flows through the Secondary Main Jet (5) to the Secondary Well
where it is drawn through the Secondary Well Tube (6). The fuel is
mixed with air that enters the tube through a series of small holes.
The source of the air is one of the Secondary Well Bleeds (7). There
are two air-bleeds; one admits air to the outside of the Well Tube and
the other allows air to flow into the passage behind the Nozzle. The
fuel, now well mixed with air, flows through the slightly up-hill
passage and exits into the Secondary Boost Venturi (3) through the
Secondary Nozzle (4).
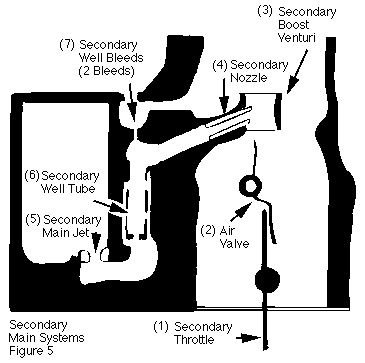
In addition to the three (3) basic Metering Systems, there are two
(2) Transient Control Systems; The Secondary Auxiliary System and The
Pump System.
Secondary Auxiliary System
During the initial stages of Secondary Operation, the air flow rate
through the secondaries is very low. Accordingly, there is not enough
pressure drop (suction) at the Secondary Nozzle to induce fuel flow.
In order to prevent a lean A/F condition that would be experienced by
the driver as a "bog" or "flat spot" on secondary
opening, it is necessary to add fuel by an auxiliary means during the
time the secondary is in the transient phase.
This is accomplished by placing a small Discharge Nozzle (2) at a
point just under the Air Valve (1). The air flow past the edge of the
Air Valve creates sufficient pressure drop to pull fuel out of the
Auxiliary System. The fuel must first pass through the Secondary Main
Jet (3) to the Secondary Well; it is then drawn through the Auxiliary
Fuel Tube (4) and exits at the Discharge Nozzle (2). There is always
an air-bleed, either in the Auxiliary Fuel Tube (near the top), or as
a separate brass restriction bushing (shown).
The flow of fuel in the Auxiliary System is enough to prevent a
lean transient on Secondary opening. As the Air Valve is opened
further by increasing air flow, the fuel flow through this system
decreases. Correspondingly, the fuel flow in the Secondary Main System
increases, providing a near constant A/F Ratio.
Pump System
When the throttle is opened rapidly, the air flow through the
engine will increase immediately. The fuel, since it is much heavier
than the air, will "lag" behind. This contributes to a
temporary lean A/F condition. Regardless of cause, a solution is to
temporarily enrichen the A/F Ratio by mechanically pumping a small
quantity of fuel into the throat of the carburetor (Figure 7). The
Edelbrock carburetor has a piston that draws fuel into the pump cavity
past the plunger lip-seal when the throttle is closing (1). Upon
opening, the lip-seal seats, allowing the plunger to force the fuel
through another one-way valve, the Pump Discharge Ball and Weight (2),
and the Pump Jets (3) into the primary throats.
The pump plunger is not driven directly by the throttle, but
through an intermediate Pump Drive Spring (4) that extends the
duration of the "pump shot" past the time the throttle stops
moving. The Edelbrock Performer Series carburetor has an external pump
lever with three hole locations for link attachment providing three
distinct pump delivery curves. This is further explained in
"Calibrating The Pump".
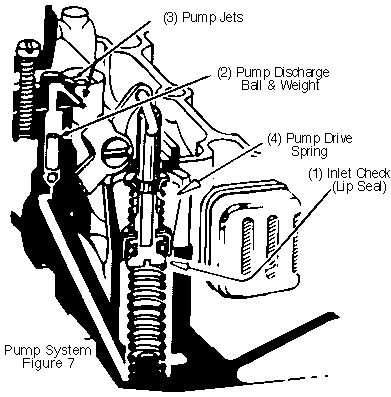
The function of your Edelbrock Performer Series carburetor is also
dependent on several external devices; the fuel pump and air cleaner.
Fuel Pumps and Pressure
Avoid extremes in fuel pressure. At IDLE, there should not be any
more than 6.0 psi; if the vehicle has an adjustable fuel-pressure
regulator, set it to 5.5 psi. With most fuel pumps the minimum fuel
pressure is encountered at high rpm and WOT. Fuel pressure should not
drop below 2.0 psi. If it does, a fuel pump with more capacity may be
required. Note that some later model vehicles (the 5.0L Ford is one
example) have mechanical pumps that will give more than 6.0 psi at
idle. The vehicle will perform well, but may be prone to stalls on
quick turns and stops with the clutch disengaged. If this problem
occurs, check the fuel pressure. If it is more than 6.0 psi at IDLE,
it should be reduced through the use of a regulator, such as Edelbrock
#8190, or by creating a restricted by-pass bleed to the fuel return
line. Edelbrock Street Fuel Pumps are highly recommended for all
Edelbrock Performer Series carburetor installations.
Always use a filter, such as Edelbrock #8873 between the pump and
carburetor. Note that a good filter is large in area, so it may be
able to transmit a significant amount of heat to the fuel. It is a
good practice to keep the filter away from heat and not allow it to
come in contact with any part of the engine.
Air Cleaners
Your Edelbrock carburetor was originally calibrated with a low
restriction open element air cleaner configuration; a 14"x3"
Edelbrock Signature Series unit. It was also evaluated for proper
metering and vehicle performance using a variety of other air cleaner
designs and will perform as intended with nearly any reasonable air
cleaner design. While the Edelbrock Performer Series carburetor does
not exhibit excessive sensitivity to the air cleaner, there are
several guidelines you should follow when selecting an air cleaner:
Running without an air cleaner is strongly discouraged for a
street-driven vehicle. Dirt and varnish will accumulate in critical
bleeds and upset the fuel metering. Dirt and debris may easily get
into the fuel bowl through the bowl vents or larger bleeds and cause a
multitude of problems.
Any calibration testing should be performed with the air cleaner
in place. Depending upon the air cleaner used, the metering
typically will be leaner with the air cleaner in place.
-
A large 14"x3" open element air cleaner, such as
Edelbrock Elite Series, Signature Series and Pro-Flo air cleaners,
offers almost no resistance to air flow. Flow bench results show
virtually no reduction in air flow. Also, this design should cause
no change to the fuel metering.
-
A 10"x2" open element design will result in some
definite air flow restriction but little change to the fuel
metering.
-
Elements smaller than 10"x2" are more restrictive
and have the most effect upon metering. The fuel metering at WOT
will be shifted LEANER, especially at higher rpm ranges.
If you have a dual-purpose vehicle that is sometimes used in
competition without an air cleaner, it may be necessary to have
two separate calibrations. If you are running a smaller air
cleaner and have optimized the WOT with it in place, do not be
surprised to find that the metering shifts RICHER when the air
cleaner is removed. This may require you to calibrate the WOT with
leaner Jets and Rods at the drag strip.
DO NOT allow the vehicle air-stream to blow across the top of
the carburetor(s) such as on an open-bodied car or full-bodied
vehicle with a tunnel-ram manifold. The flow of air across the
carburetor will result in an upset to the fuel metering that
cannot be accommodated by recalibration since the change to the
A/F Ratio will be different for every vehicle speed.
Section
2 - Base Tuning
Top of page
|